A low density, heat and chemical resistant, olefin-based TPV offering rubber elasticity at higher service temperature, in automotive and appliance parts, building materials, and sporting goods.
MILASTOMER™
Thermoplastic Vulcanizate (TPV)
Applications detail
Applications
Characteristics
- Introduction
- Characteristics
- Applications
MILASTOMER™ is a Thermoplastic Vulcanizate (TPV) elastomer, derived from olefin-based rubber and polyolefin resin. MILASTOMER™ TPVs offer the sustainability benefits of a polyolefin with the durability and flexibility of a vulcanized rubber. Produced with the olefin polymerization and synthetic rubber technology of Mitsui Chemicals, MILASTOMER™ does not require compounding or vulcanization. It is a thermoplastic resin that can be extruded, or molded into flexible parts. MILASTOMER™ is available in standard black, or in natural grades that can be easily colored.
MILASTOMER™ key performance benefits:
- Light Weight – density less than 900 kg/m3
- Heat Resistance – Higher softening temperature than other elastomers
- Rubber Elasticity – Deformation recovery superior to vulcanized rubber in long-term compression set
- Weatherability – MILASTOMER™ B (black) grades may be used outdoors over the long-term
- Secondary Processing – Outstanding vacuum forming, thermal adhesiveness, and coating performance
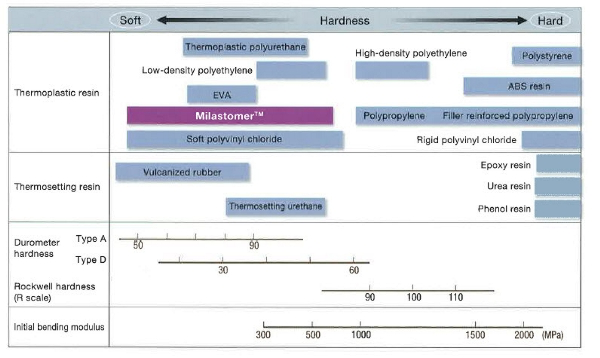
There are many grades of MILASTOMER™ available, ranging from flexible grades comparable to vulcanized rubber to semi hard grades comparable to low density polyethylene. Grades of MILASTOMER™ are available with unique characteristics, to suit specific applications.
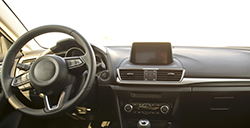
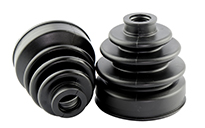
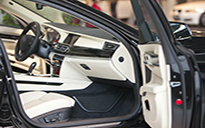
Processing
Milastomer™, thermoplastic Vulcanizate (TPV), contains no hygroscopic filler, so there is no need to dry prior to processing. The material can be processed using injection or extrusion molding.
Related Products
The thermoplastic elastomer provides a wide range of performance, aesthetic and functional characteristics and is ideal for a variety of diverse applications including automotive, building material, and consumer goods.