A narrow molecular weight distribution olefin oligomer used as a polymer processing aid, reduces torque in the extruder and allows for an increase in screw speed while operating at a lower barrel temperature.
EXCEREX™
Olefin Oligomer
Applications detail
Applications
Characteristics
- Introduction
- Characteristics
- Applications
EXCEREX™ is a high performance polymer processing aid. It is an innovative olefin oligomer, with a narrow molecular weight distribution, manufactured with Mitsui Chemical's leading edge metallocene catalysis technology. EXCEREX Olefin Oligomer acts to reduce torque in the extruder and thereby allows for an increase in screw speed and simultaneously permits operating at a lower barrel temperature. The end result is increased output, reduced heat defects (scorching) and shortened cooling cycles while maintaining finished product properties. All of this is achieved with only a small amount of EXCEREX added as a dry blend to your resin feed.

Related Products
What is the mechanism by which EXCEREX™ improves the extrusion process?
Because EXCEREX is a polyolefin with a low molecular weight and low melting point, when dry-blended with your extrusion resin it melts faster in the extrusion chamber. Due to its low surface tension, the EXCEREX flows and covers the surface of the pellets of your resin. This thin EXCEREX coating acts as a lubricant and reduces the friction between the pellets and screws, between the pellets and the chamber and between the pellets themselves.
What are the major benefits of EXCEREX as an extrusion additive?
Due to the lubricity imparted, EXCEREX:
- Enables higher screw revolution while maintaining torque level resulting in and increase in extrusion volume.
- Suppresses abnormal heat generation within the extruder thereby reducing defective product from scorching and die build-up.
- Reduces color change time, the amount of disposed resin due to dead zone and improves color change over because of its excellent wetness in terms of pigment and filler surface.
Processing and Quality Improvement
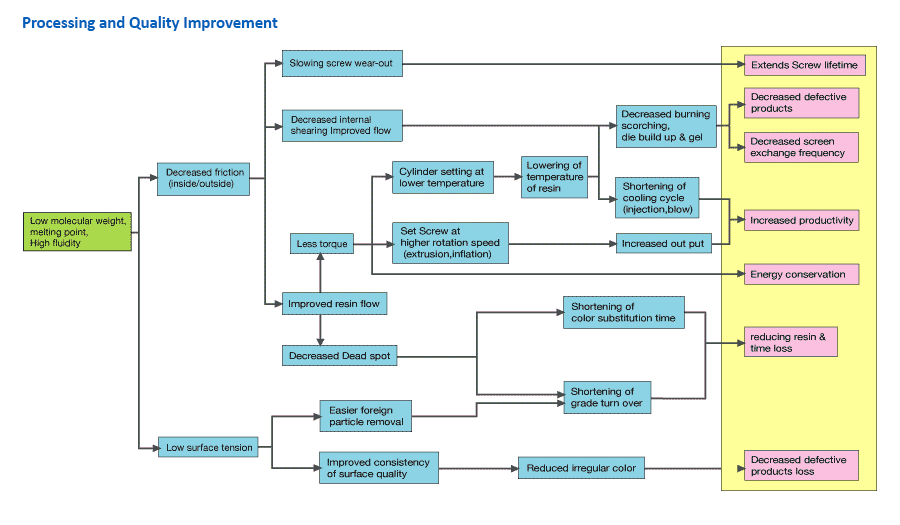
Performance on PP sheet
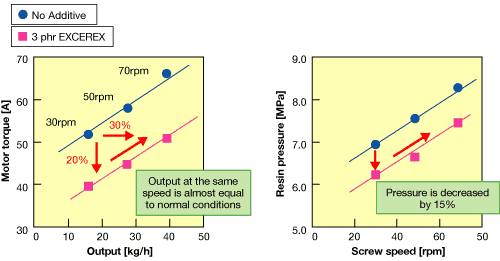
—> Increased output is over 30%
—>Decreased motor torque by 20%
Performance on HDPE Blown film
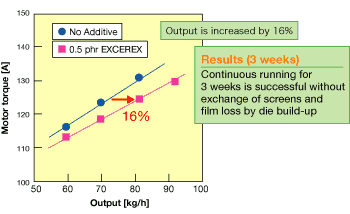
—> Output is increased by 16%
—> Does not affect film properties
—> Does not affect heat sealing and printability
Performance on PP Blow Molding
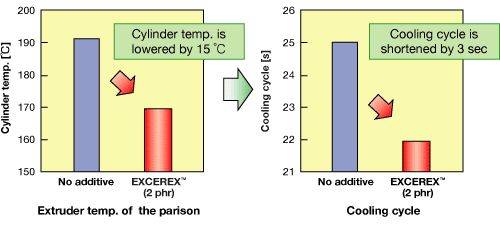
—> Processability is improved by 13%
Performance on HDPE Injection Molding
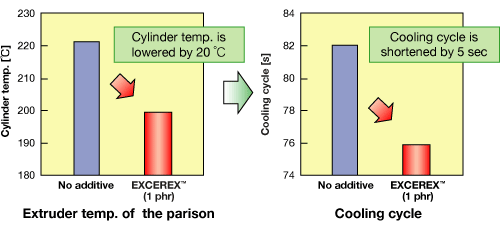
—> Processability is improved by 6%
Grades of EXCEREX
- EXCEREX is available in 3 grades with a wide range of properties. Simply chose the grade that has the best compatibility for your resin and get improved results without affecting the properties of your molded products.
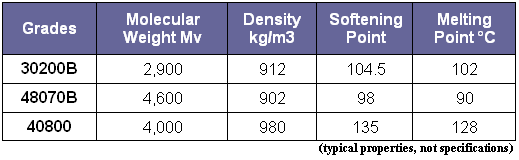
No adverse effects from EXCEREX
- With a low treat rate of 1 to 3% EXCEREX there is essentially no impact on the finished product properties.
- Given that EXCEREX contains very little extremely low molecular weight components there are no negative surface effects due to bleed out. Thus adhesiveness or paint ability are unchanged and there is no whitening nor haze.
Less Deterioration to Products
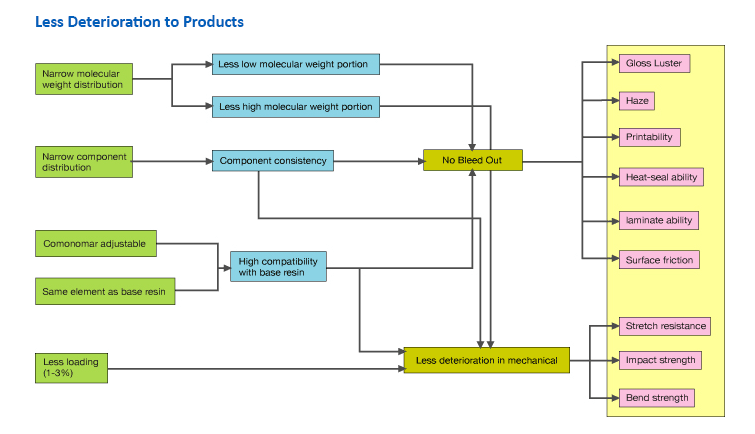
Mechanical Strength
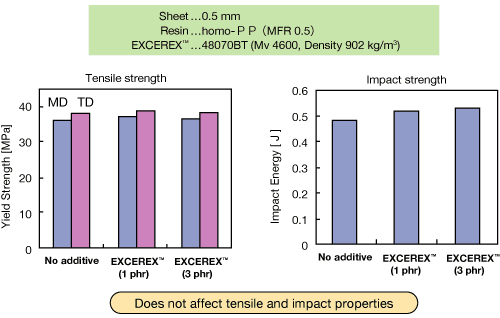
Bleed-out
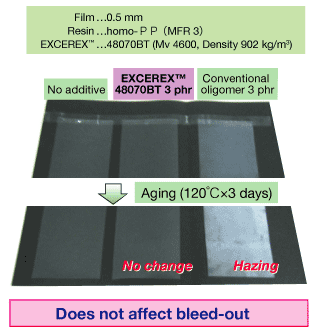
Heat Seal Strength
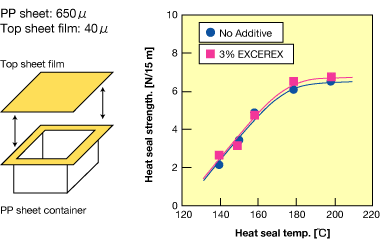
Lamination
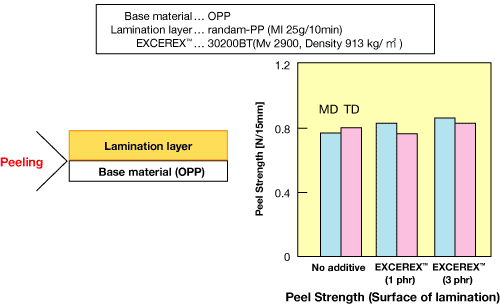
—> Does not affect lamination
Application examples as a molding improvement agent
(1) PP extrusion molding (0.5mm-thick sheet)
By adding 3% EXCEREX ™ 30200BT, extrusion volume was increased from 20kg/h to 40kg/h.
(2) PP extrusion molding (0.5mm-thick sheet)
By adding 3% EXCEREX ™ 30200BT, set cylinder temperature was lowered from 230°C to 210°C and scorching was reduced.
(3) EVA-LDPE blend extrusion molding (0.5mm-thick sheet)
By adding 2% EXCEREX ™ 30200BT, extrusion volume increased from 350kg/h to 430kg/h.
(4) L-LDPE inflation molding
By adding 2% EXCEREX ™ 30200BT, screw revolution was increased by 20%, and extrusion volume was increased from 31kg/h to 38kg/h.
(5) Biaxial drawing PP film
By adding 1% EXCEREX ™ 30200BT, screw revolution was increased from 51rpm to 62rpm, and extrusion volume was increased by 20%.
(6) HDPE blow molding (20L poly tank)
By adding 1% EXCEREX ™ 40800T, set cylinder temperature was lowered from 170°C to 150°C, and productivity was improved by 20% by reducing cooling time from 90 seconds to 75 seconds.
(7) PP blow molding (1.5L bottle)
By adding 2% EXCEREX ™ 30200BT, set cylinder temperature was lowered from 190°C to 170°C, and productivity was improved by 14% from 144 units/h to 164 units/h by reducing cooling time from 25 seconds to 22 seconds.
(8) HDPE injection molding (bottle cap)
By adding 3% EXCEREX ™ 30200BT, set cylinder temperature was lowered from 200°C to 180°C thereby reducing scorching.
Examples of the customer's applications
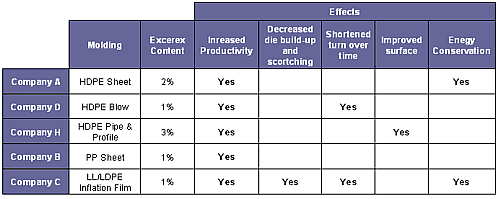